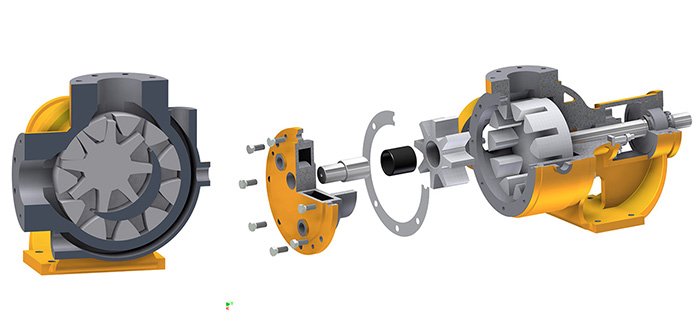
In the world of engineering, efficiency isn’t just about numbers—it’s about finding smarter, more sustainable ways to power our everyday lives. Take air pumps, for example. They’re the unsung heroes behind countless machines, from cars to factories, and getting them to compress air efficiently can make all the difference. That’s where dynamic mesh Computational Fluid Dynamics (CFD) steps in, revolutionizing the way we design and optimize air pumps. Join us as we explore the human side of dynamic mesh CFD and its role in driving efficiency and innovation in air pump compression.
The Heartbeat of Efficiency: Redefining Compression
Air pumps may seem like simple machines, but they’re the lifeblood of so many industries, powering everything from engines to manufacturing processes. Traditionally, designing a pump that strikes the perfect balance between compression power and energy consumption has been a challenge. But with dynamic mesh CFD, engineers can dive deep into the inner workings of pumps, tweaking and refining their designs to maximize efficiency and minimize waste.
Simulating Reality: Putting Fluid Dynamics to Work
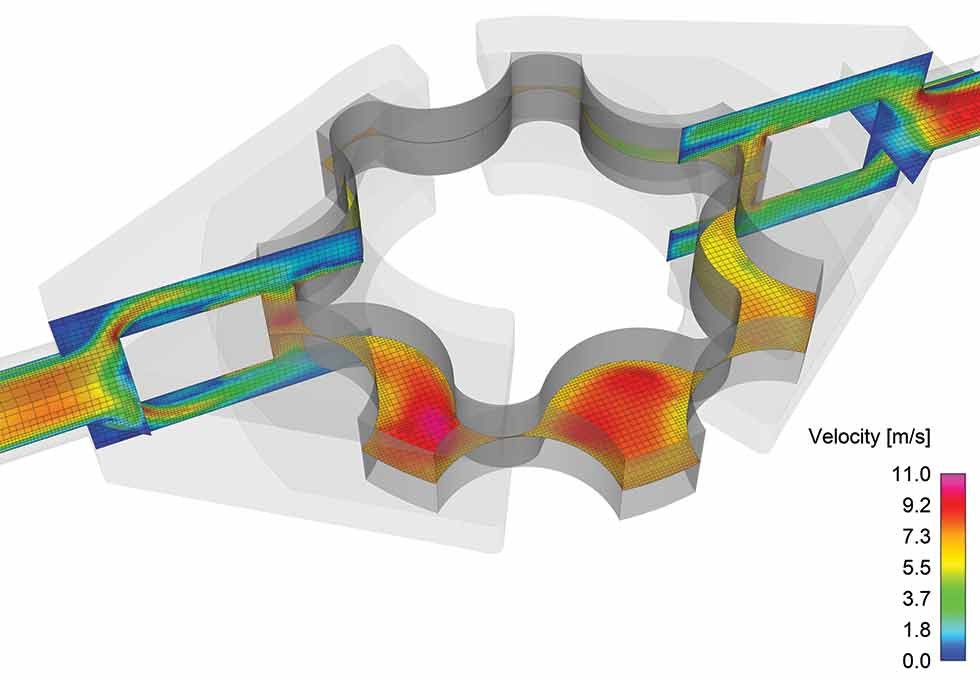
What sets dynamic mesh CFD apart is its ability to mimic real-world fluid flow dynamics in virtual simulations. Picture it: engineers sitting at their desks, watching as virtual air flows through different pump designs in real-time. By adjusting the computational mesh to match changes in pump geometry and fluid movement, dynamic mesh CFD gives engineers an unprecedented level of insight into pump performance. It’s like having a crystal ball that shows exactly how a pump will behave under any condition, allowing engineers to fine-tune their designs for maximum efficiency and reliability.
From Ideas to Innovation: Making Dreams a Reality
Dynamic mesh CFD isn’t just about crunching numbers—it’s about turning ideas into reality. With this powerful tool at their fingertips, engineers can explore a universe of pump designs without ever setting foot in a lab. They can test out wild new concepts, tweak pump geometries, and see how each change affects compression efficiency—all from the comfort of their computer screens. This iterative design process not only speeds up product development but also opens the door to groundbreaking innovations that could change the face of air pump technology forever.
Meeting Challenges Head-On: Navigating Complexity with Confidence
Air pump compression isn’t always smooth sailing. There are turbulent waters to navigate, from pesky boundary layers to tricky flow separations, that can throw a wrench in the works. But with dynamic mesh CFD, engineers can tackle these challenges head-on, armed with a deep understanding of fluid dynamics and computational power. By pinpointing potential bottlenecks and optimizing flow paths, they can ensure that every pump they design delivers consistent, reliable performance, no matter the conditions.
Driving Towards a Brighter Future: Embracing Innovation with Dynamic Mesh CFD
In the end, dynamic mesh CFD isn’t just a tool—it’s a mindset. It’s about pushing the boundaries of what’s possible, finding new ways to squeeze every last drop of efficiency out of our machines. With dynamic mesh CFD leading the way, the future of air pump compression is brighter than ever. So let’s roll up our sleeves, dive into the world of fluid dynamics, and together, let’s harness the power of efficiency to drive innovation forward.